Project
The most promising method to reuse ELT-derived rubber materials in high quality products is devulcanization. The technology could yield a product – substitute for virgin rubber, both in terms of properties and in terms of cost of manufacture. The devulcanization technology will be demonstrated through the manufacturing of two compounds using high content of reprocessed rubber feedstock from End-of-Life Tyres.
Problem Targeted
Vulcanized rubber, as elastomer, is very difficult to recycle, which is why the major part of the End-of-Life Tyres (ELT) and other rubber products are being landfilled (65%) or disposed through incineration (17.5%).
Tyres and automotive component applications, which represent some 75% of rubber demand at the European level, make almost no use at all of reprocessed rubber feedstock.
Reclaimed rubber from ELTs is used at very low concentrations in tyre manufacturing (below 5%), due to technical constraints.
Consequently, despite the increasing cost of raw materials and the environmental issues related to their consumption, the material recycling and reuse rate of rubber waste is still very low (i.e. 12.8%, decreasing to 1.5 wt% if considering the amount reused for remanufacturing high-value products like compounded General Rubber Goods – GRG – and tyres).
Proposed Solution
Rubber devulcanization is a powerful method of recycling that has an enormous potential for the development of quality raw materials from ELTs. The resulting material can be transformed into useful products which could serve as a substitute for virgin rubber.
LIFE GREEN VULCAN will integrate the devulcanization technology and produce two compounds using high content of reprocessed rubber feedstock from ELTs:
- a compound for manufacturing spring pads for cars and light trucks
- a compound for manufacturing Passenger Car Radial (PCR) tyre treads.
The innovative technology will allow an increase in the recycling rate of rubber from end-of-life tyres, while reducing CO2 emissions linked to the production process.
Objectives
Europe bases its industrial strength on a cost-efficient, secure and sustainable supply and use of raw materials. One of the aims of this project is to design a sustainable solution which will close materials loops and provide a reliable access to one of the Critical Raw Materials – Natural Rubber. By making a better use of this resource Europe can benefit both economically and environmentally.
Expected Impacts
SUPPLY EUROPEAN TYRE INDUSTRY
LIFE GREEN VULCAN will open a route to supply to the European tyre industry 200.000 to 400.000 tons yearly of reprocessed feedstock from the ELT granulates.
CO2 SAVING
This project will offer a measurable effect on both product performance properties and an overall CO2 savings, estimated in the range of 500.000 to 1 million ton of equivalent CO2 respectively.
RECYCLING & REUSE RATE INCREASE
By reducing the consumption of Natural Rubber, the risks associated with the supply of this Critical Raw Material will be decreased. An increase of 100% to 400% of the current recycle and reuse rate from post consumption tire is expected.
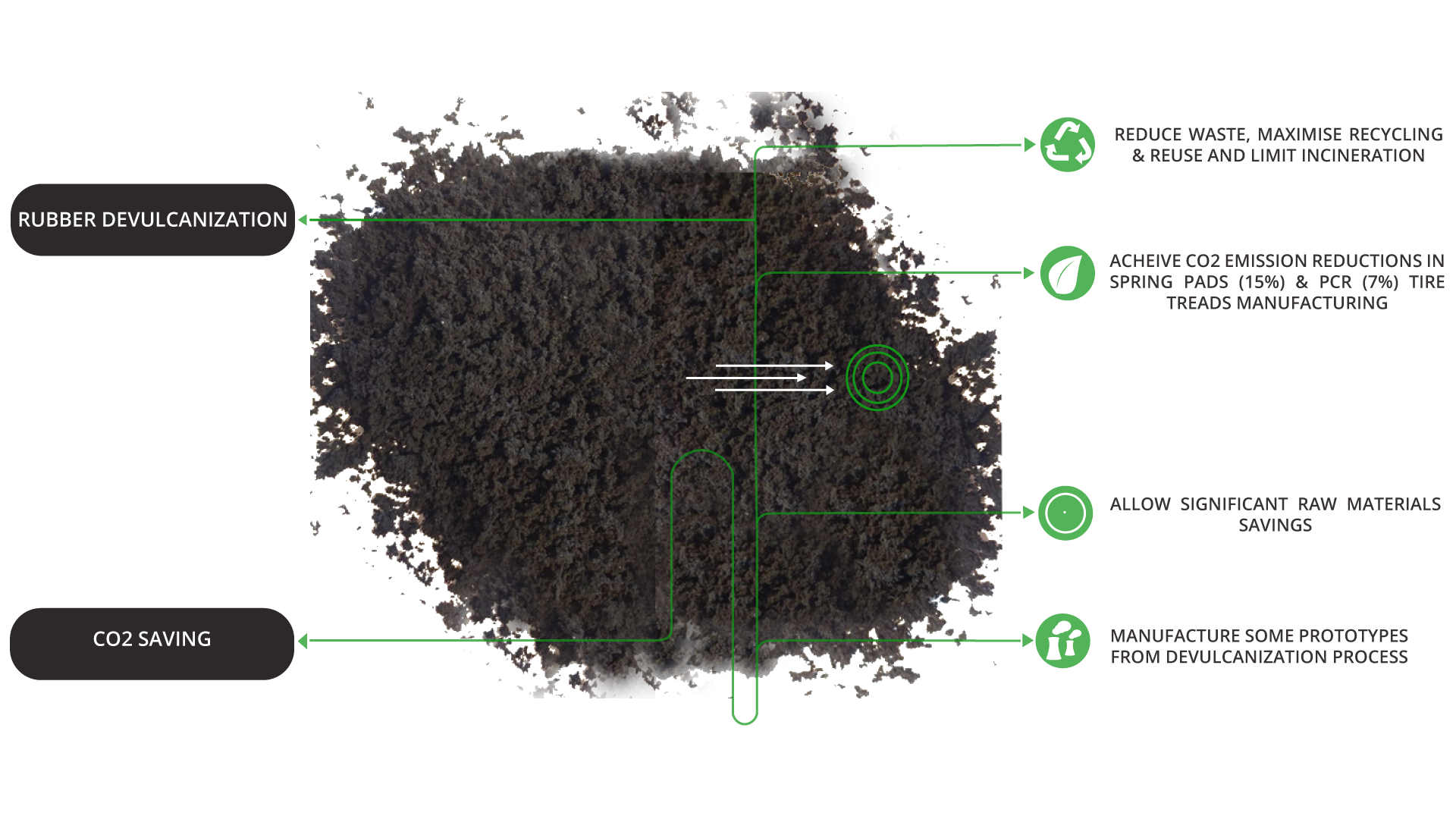
Expected Results
Development of an innovative mix of Natural Rubber/Styrene-Butadiene Rubber (NR/SBR) devulcanised masterbatches from ELTs, showing increased elongation at break (+10%) and improved abrasion resistance (+10%) with respect to the baseline rubber compounds for similar applications;
Creation of a simulation-based optimisation tool to support the development of compound recipes, maximising the content of NR/SBR-based compounds in devulcanised masterbatches, in demanding rubber applications;
Assembly of an integrated prototype plant to produce the innovative devulcanized masterbatches in slabs;
Use of the innovative devulcanized masterbatch to achieve significant raw material savings in the manufacturing of spring pads (-20%) and PCR tyre treads (-10%), meeting the same performance criteria of the related reference products;
and Demonstrate CO2 emission reductions in the manufacturing of spring pads (-7%) and of PCR tyre treads (-15%).